Professional Equipment Manufacturer










DHKC-S600 Xray counter machine
Categories:
Keywords:
Product introduction
An SMD component counter, also known as an SMT reel counter, is an essential tool for any electronics manufacturer, which allows for simple and accurate counting of small surface mount devices such as resistors, capacitors,transistors and micro chips etc. saving time and reducing the risk of errors when stocking and managing inventory.
Old Counter |
VS |
X-Ray Count machine |
|||
Item
|
Description
|
Time
|
VS |
Time
|
Description
|
Efficiency
|
Manually scan the code one by one for verification
|
10S
|
6-10S
|
Directly place the material on the workbench,press the start button to automatically scan the code, use the X-RAY perspective principle and self-developed program algorithm to quickly calculate the quantity, andupload the data to MES, ERP, and other systems
|
|
Manual loading, overhead tray, manually wrapping the material head onto the empty tray
|
20S
|
||||
Number of winding points, winding from one material tray to another
|
60S
|
||||
8 devices/8 people with 400 trays
|
1H
|
1H
|
1 equipment/1 person, 400 trays, saving 7 people | ||
Quality
|
The material tape is wrapped back and forth, and there is a risk of deformation of the IC with pins, leading to poor welding.
|
\
|
VS
|
\
|
No need to wrap, there will be no damage to the IC, avoiding the problem of false soldering. |
If the material film is damaged, the parts in the groove may fall off and be lost or stand on the side, leading to the risk of empty suction or throwing of materials in subsequent patches.
|
\
|
\
|
The parts can be scanned with the incoming material intact, without damaging the material film. The parts in the material groove
are not side standing to avoid problems such as throwing and air suction, reducing material loss.
|
||
MSD parts need to be unpacked, which increases the exposure time and causes moisture to the materials, resulting in quality hazards
|
\
|
\
|
MSD parts do not need to be unpacked, reducing exposure time, avoiding material moisture, and not causing quality hazards. | ||
Misjudge
|
There are multiple processes that rely on manual labor. Manual reading and recording are prone to errors, manual label changes are prone to confusion, manual input of system update data is prone to errors, and empty material slots are also included in the inventory quantity.
|
\
|
VS
|
\
|
Fully intelligent inventory, intelligent code scanning, automatic uploading, less reliance on manual labor, and empty material slots will not be included in the inventory quantity. |
Summary: Traditional counters are time-consuming, inefficient, have high quality risks, and are prone to errors. The efficiency of the intelligent material dispenser has been improved by more than 5-7 times, without quality risks and avoiding errors.
|
Detailed Images:
1. Compared to traditional counters, intelligent counting machines do not require the opening of sealing material trays and transit material trays.
2. Adopting a side window type closed tube X-ray source, it has a long service life and is maintenance free.
3. The flat panel detector adopts a 14 inch ultra clear screen, with clear imaging and no deformation.
4. The diameter of the measurable material tray is 7-14 inches (with 4 7-inch material trays or 1 14-inch material tray).
5. Accelerated inventory speed and reduced labor costs.
6. The drawer automatically enters and exits, and the grating automatically senses, preventing hand gripping and facilitating retrieval.
7. Algorithm and innovative detection environment with AI functionality.
8. Interface with MES/ERP/WMS and other system data, exchange data in real-time, and timely upload and update material information.
9. Full induction recognition of material labels, error and mixing prevention, and real-time docking with printers.
10. Designed according to the human sitting posture, it is not prone to fatigue, occupies less space, and is easy to move.
11. Suitable for various types of SMD components, SMD devices above 01005.
The foundenmental that SMD Xray counter DHKC-S600 works on
Product application:
Those components which we can count, including them but not only.
The X - ray counter machine has emerged as an invaluable tool in the realm of Printed Circuit Board Assembly (PCBA) detection, repair, and the maintenance of electronic components on chips and circuit boards.
In PCBA detection, the X - ray counter machine provides a non - destructive means of examining the internal structure of the board. It can accurately count and analyze X - ray transmissions through the PCBA. This allows technicians to identify hidden defects such as broken traces, solder joint voids, or misaligned components that are not visible to the naked eye. For example, in a densely populated PCBA, it can detect minute cracks in solder joints that could potentially lead to malfunctions.
When it comes to PCBA repair, the information obtained from the X - ray counter machine is crucial. Technicians can precisely locate the problem areas, whether it is a faulty chip or a defective connection. This targeted approach not only saves time but also reduces the risk of further damage during the repair process.
For chip and electronic component repair on the circuit board, the X - ray counter machine offers detailed insights. It can help in determining if a component is damaged internally, perhaps due to overheating or electrical stress. By counting and analyzing the X - ray interactions within the component, technicians can decide whether to replace or attempt to repair it.
In conclusion, the X - ray counter machine has revolutionized the way PCBA, chip, and electronic component repairs are carried out. Its ability to provide in - depth and accurate information makes it an essential asset in the electronics repair industry.
FACTORY WORKSHOP










CUSTOMER TRANSACTION
Adhering to the business principle of mutual benefits, we have had a reliable reputation among our customers because of our professional services, quality products and competitive prices.

CUSTOMER TRANSACTION
We welcome customers at home and abroad to visit our factory to reach long-term cooperation and create success together.

FAQ
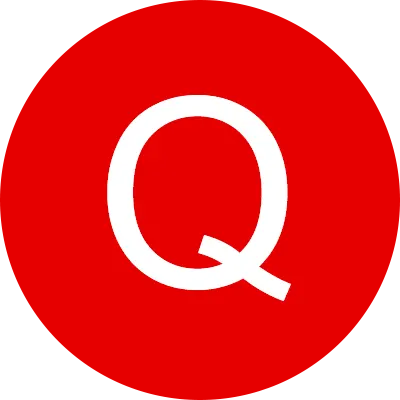
Can you make a proof for using automatic soldering station:
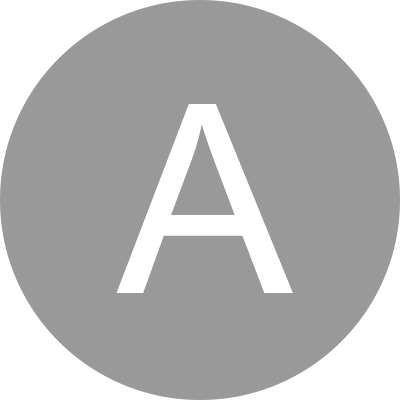
Yes, please send us your motherboards and components,we can even customize a jig/fixture which will hold your motherboard & components on Machine’s table for soldering.
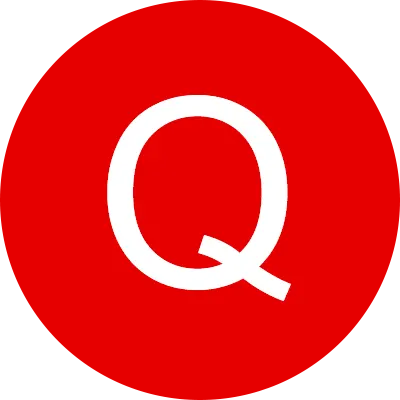
What is a BGA reworkstation?
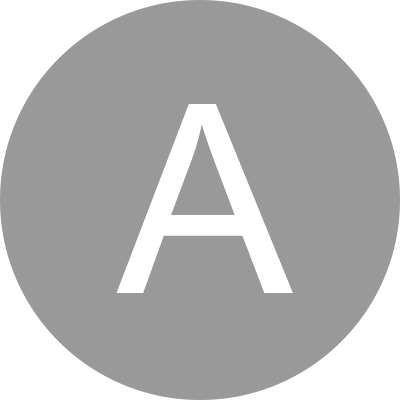
Dinghua BGA rework stations, featured with 3 independent heating-area, PID controlling temperatures, real-time curves displaying on touchscreen, is a station used for various chips and a few components desoldering or soldering.
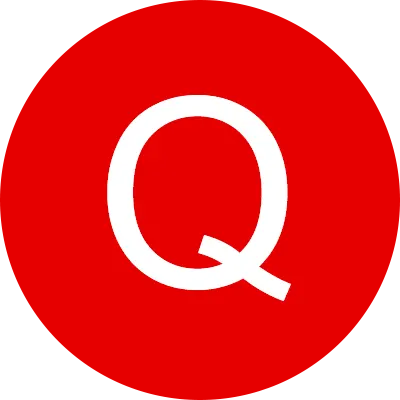
Are you a manufacturer or a trading company?
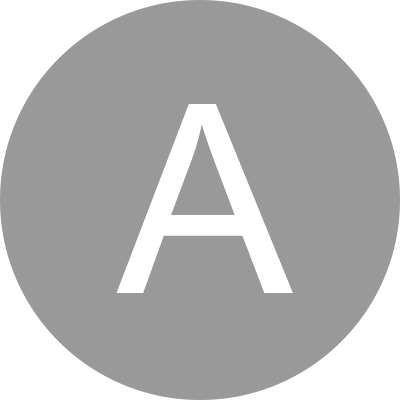
We are a leading manufacturer of BGA rework station, Xray inspection machine, Xray counter machine and automation equipment etc
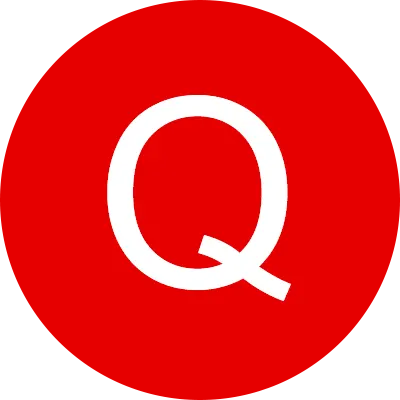
Where is your factory?
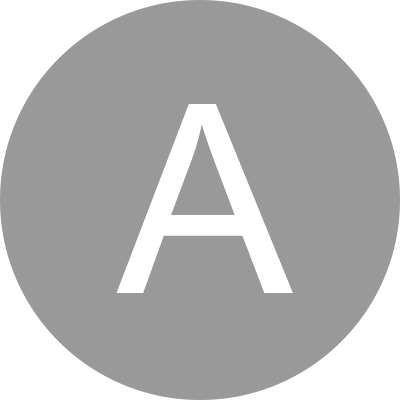
We are located at 4F 6B, Shengzuozhi Technology Park, Xinqiao, Bao’an, Shenzhen, Guangdong, China
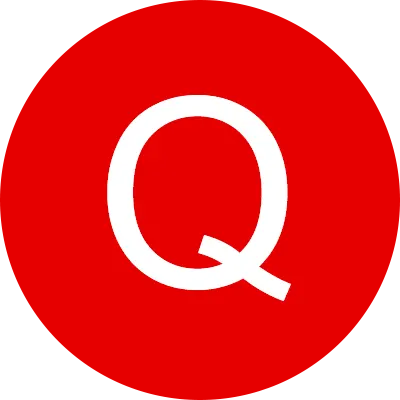
Are there over-seas after-sales service centers?
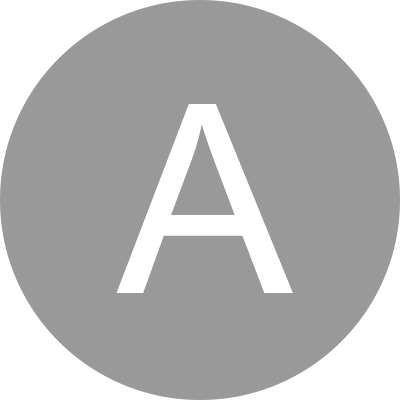
BGA rework station, Xray inspection machine, Xray counter machine and automatic soldering station consist of modularized structures, which are simple to change. So, if machines have a problem, changing its relevant part. We don’t arrange after-sales engineers to always live overseas, but, if our customers need extra service, our engineers can go to on-site
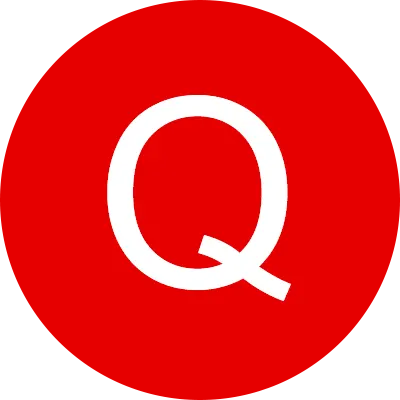
Have you had experiences cooperating with cross-border enterprises by today?
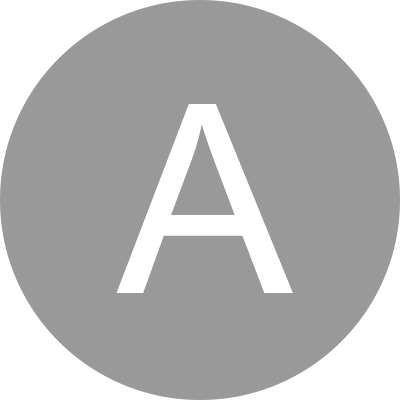
Yes, we do. Such as, Google, Foxconn, Micron, Vestel, Huawei, Kinpo and BYD etc
Online Message